Corrosion monitoring - why coupons are a bad solution
- Guillaume Labrouze
- Sep 1, 2022
- 3 min read
Updated: Sep 16, 2022
If you are reading this article, that is probably because of its (slightly) provocative title. The #corrosion coupon is a great tool for long term corrosion monitoring. But its drawba
cks are usually ignored by the end users. The consequences: high risk exposure of the personnel, wrong interpretation of results and abandonment of those systems.
This article explains the benefits, drawbacks and common mistakes related to coupons. With all that in mind, you will understand that many factors shall be taken into consideration prior to their use.
There are many more factors to be considered when engineering such solutions (size of access fitting, type of access fitting, material selection, pressure service, etc). The intend here is not to design a system, but to understand its purpose and its limits.
Coupons?
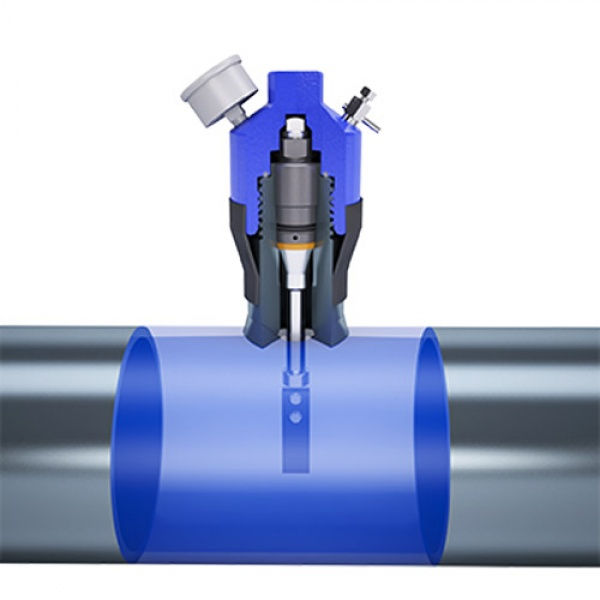
Corrosion coupons are small representative pieces of metal used to evaluate system corrosivity, material performance, and corrosion inhibitor effectiveness. The coupons are placed in strategic locations throughout the system.
They are installed inside the pipeline (via an access fitting welded on the pipeline) and are retrieved every 3 or 6 months. Weight loss and visual aspect of coupons give an estimation of corrosion rate and allows an identification of the corrosion mechanism.
The advantages of a coupon system:

it is simple and inexpensive
it requires a minimal amount of attention once in place
it provides physical evidence of corrosion when removed from a system
it allows an analysis (visual) of corrosion products
The drawbacks:
Coupons are installed in live pressurized systems: only qualified and well-trained personnel should be allowed to install/retrieve them. The operator shall be considered as highly exposed and necessary safety precautions shall be taken. See here for safety alerts related to corrosion coupons: link 1, link 2.
Coupons must not cause turbulence in the flow stream, or erosion effects will falsely increase corrosion rates.
While holding the coupon during its installation, handprints or sweat can increase the corrosion rate while a greasy thumb print can protect it from corrosion.
Access space to manipulate the retrieval tool is a major constraint. An improper location can result in an unusable coupon system or in unsafe conditions for the operator.
Coupons shall not be installed on piggable lines, otherwise, the pig will be stuck, and the coupon will be damaged. A flush type coupon can be used for this type of line, but this type of geometry has limitations (size, type of detected, limited contact with water).
Environment: the fluids to which coupons are exposed affect corrosion rates. A piece of paraffin or an oil film coating can give inconsistent results.
Period of Exposure: a short-term exposure might be misleading. The coupons need time to be relevant, usually. They should be retrieved every 3 to 6 months. However, in case of aggressive fluids, it may be already too late to mitigate the damages.
Occasionally, corrosion rates measured by coupons fluctuate. Such fluctuations can be misleading. For example, a coupon experiences corrosion during the month that a particularly aggressive fluid (possibly work-over chemicals) flowed in the line. Although the fluid may now be not corrosive, the coupon indicates a high corrosion rate for the line during the monitoring period.
The most critical problems encountered in the handling of corrosion coupons:

Improper coupon size and location: the sensitive element (coupon or probe) shall be in contact with liquid water: its position depends on the flow.

Improper coupon shape. Each coupon geometry has a purpose (flush, strip, cylindrical, drilled).
Recording errors in coupon number reporting.
Recording errors in coupon weight.
Recording errors in coupon installation and removal.
Recording errors in coupon exposure location.
Improper storage of new coupons allowing for atmospheric corrosion and contamination.
Improper manual handling that results in contamination of coupon surface by foreign agents (oil, dirt, etc.) or sweat.
Mechanical damage of new coupons that result in weight loss by surface abrasion and in stress zones that are more susceptible to corrosion action.
Improper mounting that results in loss of coupons if the bolts are not properly secured.
Improper alignment when in service that allows excessive erosion and corrosion product removal.
Improper cleaning procedures that result in incorrect weight loss because of: incomplete removal of corrosion product, removal of metal by excessive cleaning, incomplete drying of cleaned coupon.
About Sanorah
Defining a proper corrosion monitoring strategy is complex. This is where #integrity specialist companies like #Sanorah provide a clear added value. For each pipeline or installation, there is a cost-optimal monitoring solution which provides the proper piece of information about the corrosion activity and how to mitigate it. Contact us on Linkedin or on our website.
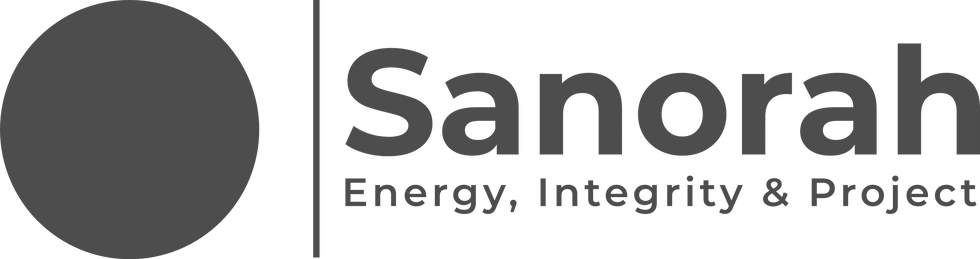
コメント